This is the first of a series of posts titled “Gems of Metal Cutting” in Bengaluru, India.
Why this initiative?
India’s defence manufacturing is set to grow.
In this upcoming boom, it is technologists who will be first responders, and who will drive the manufacturing.
In this series of articles, you will get to know about such Gems who are experts, tackle problems head on, and above all who have shown a higher level of sincerity.
The first Gem we have chosen for this series is Mr. Kannan, who apart being an expert in designing and manufacturing various cutting tools, is one of the nicest person you will ever meet.
Which means he carries two brands. One, the metal cutting stalwart brand, and two, the nice person brand.
Let us quickly discuss the nice person brand. In today’s world, meeting people in the manufacturing world can be quite challenging as everyone is looking to their interests and the work culture is such.
But, with Mr. Kannan, it is a different experience. You will want to see him everyday in the shop floor, as his presence adds immensely to the tech discussions. He is knowledgeable, and is not miserly in sharing his knowledge. Don’t let his affable nature mislead you.
Most Engineering Departments work in the following way. Get the component drawing ready, make a judgement of which machines available in the shop floor will do the job of cutting this component, create the first or set of toolpath(s) depending on the complexity of the profile, create the NC program and do a trial run.
From then on, with the goal of finalizing the program in the minimum number of runs, trial runs are done and the final NC program is released to the shop floor.
Most of the entire shop floors operate in this way.
This is highly unsuitable for aero and defence manufacturing. However, very suitable for non critical auto components. Simply, most of the components (not all but most) have simpler profiles and generous tolerances.
Mr. Kannan, – Intro
It is here technologist’s services like Mr. Kannan’s are indispensable.
If shop floor engineering teams can include him in the discussions he will bring such a wealth of experience into the engineering section that the efficiency of the engineering teams changes in instantly.
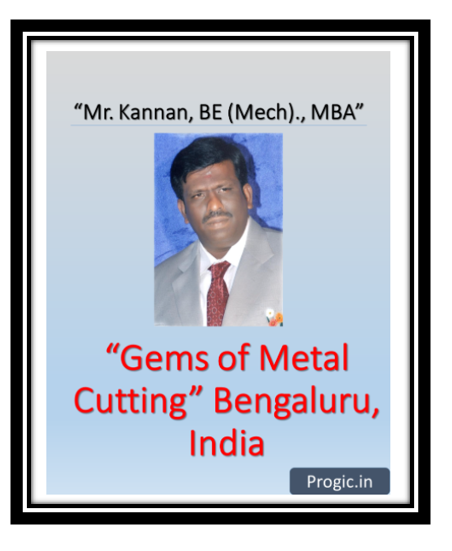
For him creating a component is a creative experience, each time, every time.
The consequence of this approach is that shop floors can take up more challenging components and hence quote better prices and more profits.
People like Mr. Kannan are rare, and the metal cutting industry should make efforts to preserve such talent.
Unwilling to sacrifice his freedom, he has not taken up a job, and operates as a consultant. Even in these trying times of Covid-19 and its variants, he has regular work.
So, how did Mr. Kannan start his journey in Metal Cutting and how did he acquire such expertise?
With his job as a Apprentice in Kennametal, at an young age, Mr. Kannan started doing what he likes most, creating components. An astute engineering mind, and academically strong, an young Kannan, could sense that working in the shop floor and being responsible for all machining activities is the key to achieve his dreams.
So, what are his dreams?
His only dream is to simply be creative in the metal cutting engineering world everyday, 365 days. Over the years he has acquired expertise in electronics and automation too.
I was able to catch up with Mr. Kannan, for a quick interview, which because of his knowledge and experience, extended a bit longer. He was kind enough to let me ask all questions and answered them patiently.
Interview
Q: Mr. Kannan, Thank you for giving an interview to us. May we know where are you originally from?
I am a third generation Bangalorean born and brought up in this lovely Garden city. I love this city, culture, people, tradition, food, and temples.
Incidentally, my father’s grandparents shifted to Bangalore in late 1890s from Tamil Nadu.
Q: Were you interested in shop floor work since your engineering days?
Much before college, I was interested in Mechanical things. My Father was an employee at HAL, and he used get HAL calendar listing Aircraft for each month, and I started asking father how an aircraft is manufactured.
At home, I would help in repairing Rallis bicycle, winding of wall clock, alarm clock, winding of automatic wrist watch, come to think of it, I was always curious about how things work, my father also used to take our family to air shows which satisfied my appetite. All these collectively ignited a passion for me in Mechanical Field.
It was natural that I tried join GT&TC as a tool and die maker, passed in the entrance theory, but failed in the practical entrance test. Meanwhile, secured a full time apprenticeship as a machinist in Widia India Limited, now called Kennametal India Limited. Here, I won the Gold medal for skill Olympics in Calcutta conducted by CII (Confederation of Indian Industry) and selected to represent India in Work Skill Olympics in Paris.
Based on my work, I was given an appointment in Widia, and I joined Diploma in mechanical engineering in SJP, Evening College. I graduated with distinction, and paved the way to join BMS Evening College for Mechanical Engineering branch.
My dream was to pursue an MS in Mechanical Engineering in Germany, which was expensive for me.
So, here I am.
Q: How has metal cutting changed over the last 25 yrs?
In my 25 yrs experience of working in the shop floor, the making of cutting tools has changed very much. For a number of years, we have been using tools made of High Carbon steel in fitting shop like hacksaw blades, files, chisels. Then in conventional machines like milling , turning we were using cutters, turning holders made of HSS of different grades like M42, M35, M2.,
With the advent of CNC machines, whose purpose was to increase production, Tungsten Carbide tools both solid and brazed type tools appeared, and subsequently for consistency and quick change we went in for insert type cutters, holders.,
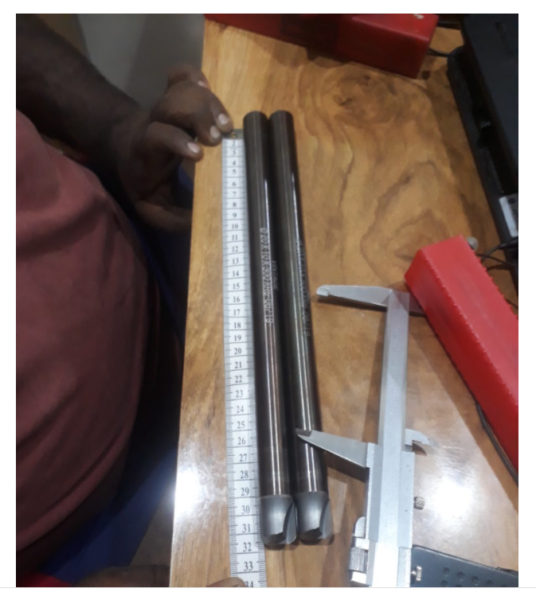
We also adopted ceramics for turning and milling applications, but the major drawback was it used to chip off due to shocks and intermediate cuts like in milling application, so we tried using it for wear parts. This problem of brittleness was over come in the Cermets which is ceramics reinforced with metal to increase toughness, the cermets were of greater use in brazed reamers, turning applications where we need to achieve the tough CPK, PPK values.
To again increase the life of tools we adopted different coating technologies and also adopted the coolant through technologies to reduce wear of the cutting points. Another material like CBN drills, inserts were introduced to increase further tool life. The latest material which is making noise is PCD-poly crystalline Diamond which is used in hole making in aluminum and non-ferrous parts.
Today, many alternatives are available. Numerous non-chip forming metal cutting processes like, laser cutting, plasma cutting, water jet cutting, erosion, additive manufacturing, wire-cutting process, to obtain accuracy, precision, complex profiles with minimum time and material have appeared. To conclude, we can say that the Metal Cutting industry is constantly evolving, people are going for research in newer technologies, process.
Q: Tell us your methodology for manufacturing a special purpose cutting tool?
The Methodology for Manufacturing a Special Purpose Cutting Tool are:
- Initial Meet with the Tooling/Design/Production Personnel and learn the cutting Tool Requirement.
- Study the component Drawing, Process, Material to be cut, component holding, Cutting Tool GPL (Gauge Plane Length), Accuracy to be achieved, Adherence to CPK, PPK values,
- Selection of Cutting Tool material depends on Hardness of the Material to be cut, whether coolant used, dry cutting, process.,
- Next check the L/D values and check the stiffness of the Cutting Tool. If nominal value is not achieved we will have to go for Composite material. (for example: Long Brazed Reamer with more than L/D value 10 has to be infused with carbide in the core of Steel blank to increase stiffness).
- Next Process is to Design the cutting tool, taking into factors of holding like integral tool-BT40, MT2 ., The cutting tool rake, clearance, flute helix for a particular material has to be designed, to reduce wear we need to go for a suitable coating and through coolant required or not.
- Initial Tool Design drawing has to be discussed with the customer, need to take their suggestion, improvements, changes, past experience, faults. And incorporate in the drawing.
- Next after the tool is designed, DAP (Drawing Approval Process) has to be taken from the customer.
- Based on the design, accuracy and complexity of tools, we need to decide whether to manufacture in T&C CNC machine, Profile grinding, special erosion, laser cutting, wire cutting is required. Usually the accuracy and economics decides the type of manufacturing process of Tools.
- Next a single tool is manufactured and given for the trails, if it is approved, all the drawings, process , tool material., freezes and the control drawing is stored both in hard and soft Copy format.
- Now a days, CPC –Cost per Component is the major criteria for the Tool Prove out Process.
- The concept of Quality, TQM should be followed religiously right from design stage to dispatch stage to the customer.
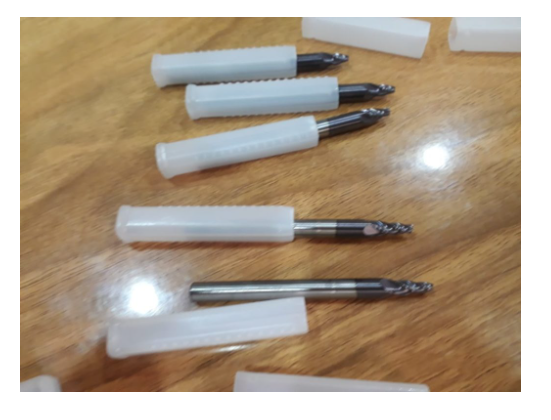
Q: Tell us the state of the Component Manufacturing Industry today?
The present state of the component manufacturing requires engineers with experience to produce a quality component consistently, economically in the minimum possible time. The planning of cutting tools, fixtures, checking gauges, programming of CNC program, prove out , supply initial components for PPAP has to be doing in a least possible time to get the component orders. Presently, we don’t have many engineers to do multitasking. So, planning of tools, fixtures, checking gauges is allotted to different departments. Finding a coordination between all the departments in union is what a component manufacturing team has to aim for. Presently we don’t find more production quantity components, engineers need to adopt to batch productions every day.
With the advent of electric vehicles, the component manufacturing of automotive parts needs to adapt to these new environment and evolve. Also with the introduction of Robotics, there is less intervention of man, the need of the hour is constant training, adapting newer technologies, process, and inspection methods to stay in the race of components both for Automotive, Aerospace and Defence components.
With websites like these, which are highlighting the defence manufacturing industry, and huge upcoming opportunity in defence sector which Mr. Krishna is spreading through his talks and seminar, opportunities for mechanical engineers are set to increase.
But, we need to upgrade ourselves to manufacture components and use machines like DMG Mori, Traub, Doosan, Makino, and others.
Q: Tell us about some interesting cutting tools you have manufactured?
Some of the interesting cutting tools I have manufactured are mainly for Aerospace and Defence component manufacturing, so of the projects which I remember are:
- Combination step reamers for Honeywell project.
- Long series brazed end mills for ISRO project.
- Ball nose, Bull nose, special tools for machining Titanium Rotomast of Helicopter.
- Complicated profile Tool for Titanium machining of Engine Mount of LCA project.
- Special combination drill with chamfer for composite machining of NAL project.
- All special tools for Aluminum machining of Mahindra & Mahindra Naval project.
- Long series Tap (180mm long) of HSS material for deep-hole tapping of Aerospace component.
- Profile tools in HSS, Carbide for many aerospace projects.
- Special HSS cutters for Thread Milling applications.
- Special Carbide punches and dies for powder compacting application.
- De-vibrating carbide brazed to steel boring bars.
- Concave radius tool with 20 micron accuracy for machining convex surface on black box.
- Converted many types of brazed special combination tools to insert type tools for faster indexing and avoid waiting period of regrinding of brazed ones.
Some pics of special purpose cutting tools created by Mr. Kannan.
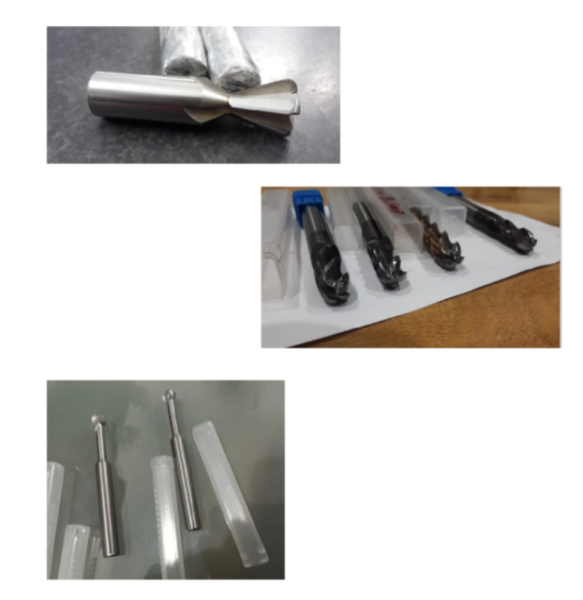
Many special cutting tools for import substitution, and to reduce cost, delivery and lead time.
Q: Which was your most challenging cutting tool project?
The most challenging cutting tool was that of a Profile tool for engine mount of LCA project, where the radius tolerance was less than 50 microns. Even after achieving this on tool, the profile to be achieved on the job was a difficult one. We achieved this finally with repeated trials.
Q: I came to know that you are into automation projects nowadays. Tell us about your experience in automation?
It was accidental, an acquaintance asked me to help him as he was building a “Automatic Powder to Pellet Machine”.
I started working with him during my free time on the automation project, and we together a built a machine which is explained in this diagram.
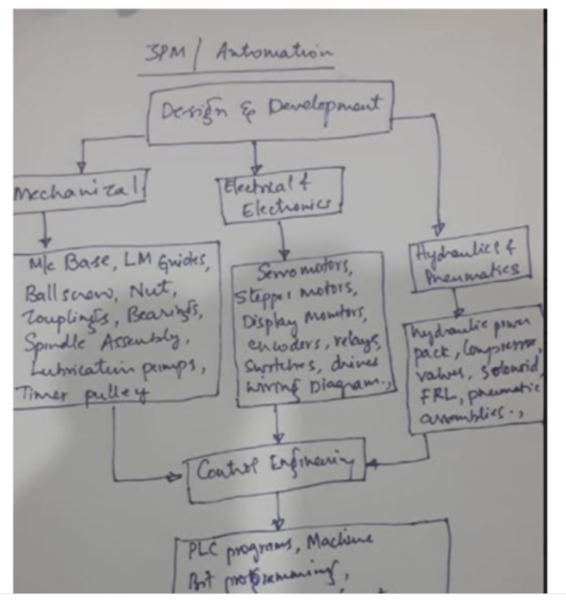
This machine is now commercially available and being sold, which is a satisfying experience for any technologist.
Time had come for us to leave.
Thank you, Mr. Kannan, for your time and detailed replies. Wishing you the best, and requesting you to support our website and channel.
Mr. Kannan is our “Stalwart of Metal Cutting and Automation in Bengaluru, India”.
How did you like our selection, questions and answers? Let us know in the comment section below. You can also address your question to Mr. Kannan, directly in the comment section. He will answer you personally.
Would like to contact Mr. Kannan? Do give us a call at: 091-98451 65193. We will put you in touch with him.